BISS – A division of ITW India participated in the 3rd International Conference & Exhibition on Fatigue, Durability and Fracture Mechanics between 29-31st August 2019 at Visvesvaraya Technological University, Karnataka. The event was successful and witnessed participation from Industry, students and researchers from universities and research labs across the country. In this event, Industrial experts and academicians came to a single platform & facilitates exchange of ideas and advancements in the field of fatigue, durability and fracture mechanics applications.
BISS presented its capability in mechanical testing and exhibited during the exhibition. BISS also introduced its latest development -“SmartConnect™”, an IoT based application for remote monitoring applications. Visitors showed interest with BISS product offerings and visited the factory during the available time.
BISS at ADMAT2019, 23-25 September, Courtyard by Marriott, Hyderabad, India – 2019
BISS – A division of #ITW India participated in the ADMAT2019 exhibition and conference between September 23-25 at Courtyard by Marriott, Hyderabad, India. The event was successful and witnessed participation from Industry, students and researchers from across the country. BISS presented its capability in mechanical testing and exhibited during the exhibition. BISS also introduced its latest development – “SmartConnect™”, an IoT based application for remote monitoring applications. Visitors showed great interest in BISS product offerings
Happy New Year from team Instron India! – 2020
The BISS Team starts Leap Year 2020 fully integrated as part of Instron, the world’s most trusted brand in materials testing. Instron now has the largest manufacturing and technical sales & support resources for supporting our customers in India.
LCF Testing Systems
Example
Single Peak Velocity Cyclic Testing for Dampers: Reduces Cycle Time, Increases Throughput
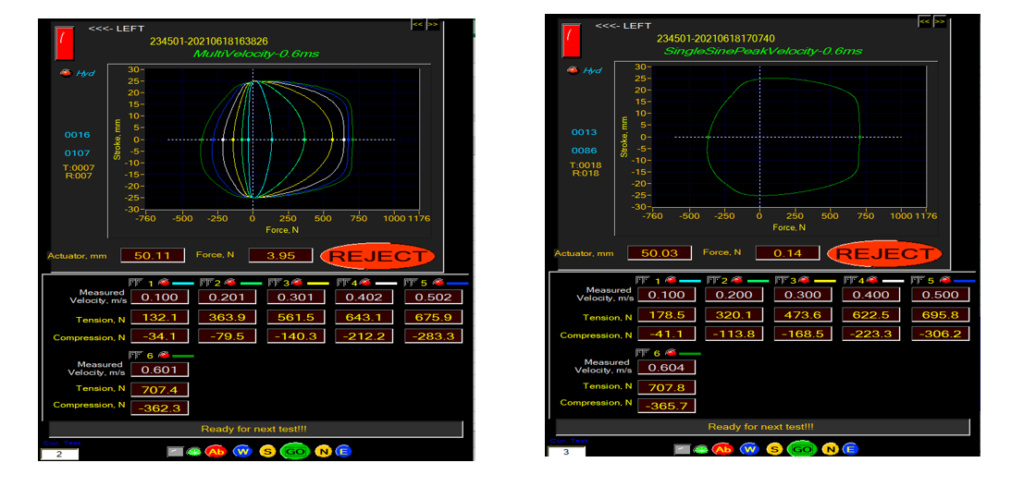
Over two million tests are performed every month on over 100 BISS supplied shock absorber test systems with practically all global manufacturers. The evolution of superior shock absorber test technology involved many technological innovations, some of which impacted the entire BISS range of test equipment. The shock absorber industry now has the benefit of yet another important innovation named ’Single cycle peak velocity testing’.
Available cycle time for production line QC testing is restricted to between 7 to 20 seconds depending on part type. A typical shock absorber for its evaluation of damping characteristics needs to be tested at multiple velocities, e.g., 0.1 m/s, 0.3 m/s, 0.5 m/s, 0.8 m/s and 1 m/s (on a test system rated to deliver max. velocity of 1 m/s). Latest BISS software solution extracts damping force readouts for all these velocities from just a single stroke of the shock absorber. The dramatic reduction in test cycle time allows manufacturers to boost production in this highly competitive market.
Noise Detection Test System: Minimizes Rejects, Restores Brand Image
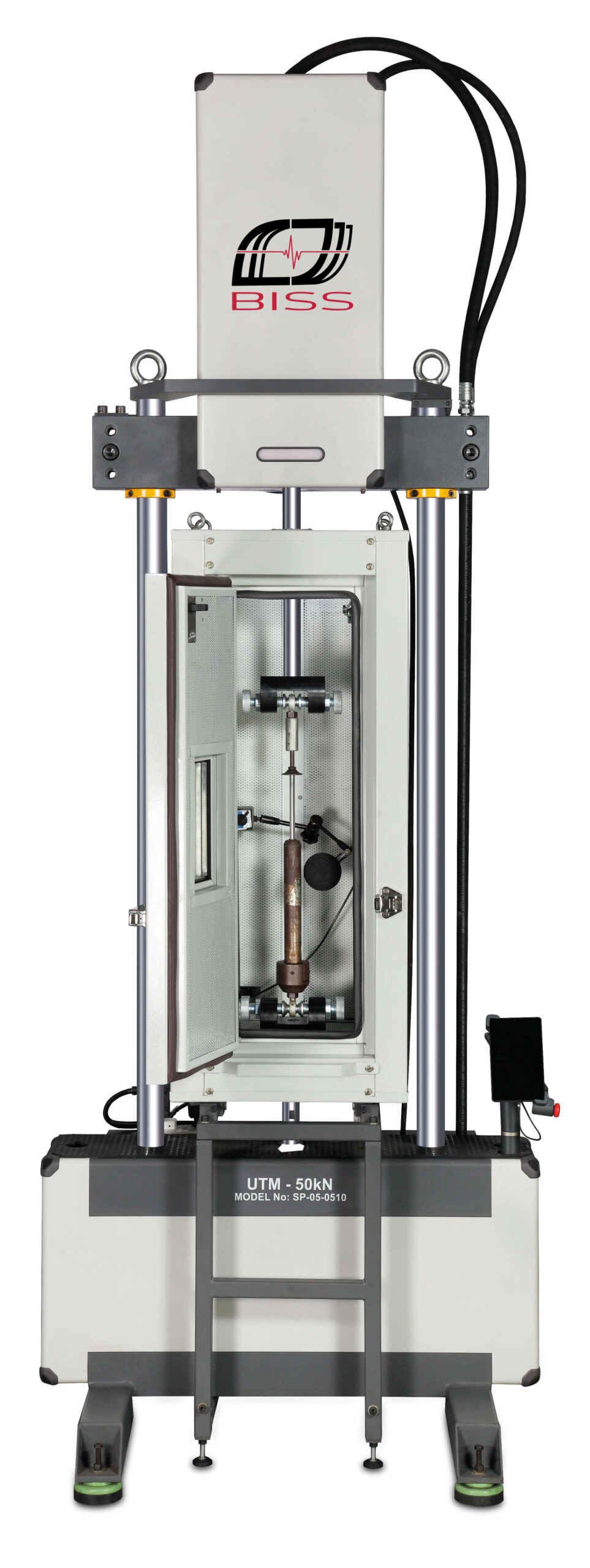
Shock absorbers are prone to transmit structure borne noise to the vehicle that is increasingly becoming apparent and is of concern to the drivers and the passengers. Structure borne noise is perceived to be a quality deficiency or even a vehicle malfunction that adversely affects the brand image of the vehicle.
BISS noise detection test system helps in identifying the specific noise in these shock absorbers that can be corrected before being put in use. This helps both the auto companies and component suppliers in reducing rejections.
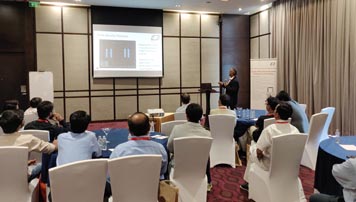
Nuances in Shock Absorber Testing, Hilton Garden Inn, Gurugram
BISS – A division of ITW India organized an one day seinar on “Nuances in Shock Absorber Testing” ,
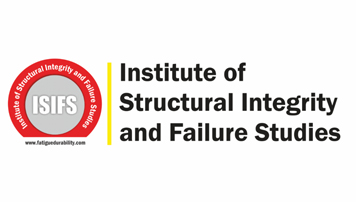
BISS at Fatigue Durability India, Visvesvaraya Technological University, Karnataka
BISS – A division of ITW India participated in the 3rd International Conference & Exhibition on Fatigue
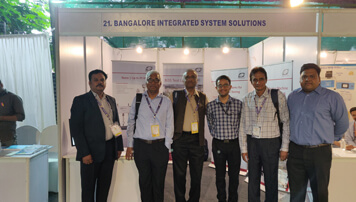
BISS at ADMAT2019, Courtyard by Marriott, Hyderabad, India
BISS – A division of #ITW India participated in the ADMAT2019 exhibition and conference betweenr first post. Edit or delete it, then start writing!